From Paper to Digital: A Roadmap for Modernizing Work Instructions
Still relying on manual and paper-based work instructions? Making the switch to digital work instructions is easier—and more critical—than you think!
December 17, 2024
The manufacturing industry is at a crossroads. While technology has transformed many facets of production, a surprising number of organizations continue to rely on printed work instructions for their assembly process. This outdated approach isn't just a minor hiccup—it's a significant roadblock that hampers efficiency, escalates costs, and increases the likelihood of errors. Despite its widespread impact, this problem has been largely overlooked for years, partly because it’s deceptively complex to solve.
Digitizing work instructions isn't just a trendy upgrade; it's a fundamental shift that empowers manufacturing companies to enhance operational efficiency, reduce expenses, and minimize mistakes. It’s Industry 4.0 at its very best.
But let's peel back the layers. Beyond the obvious hurdles, there are hidden, underappreciated downsides to sticking with paper-based, analog work instructions. Understanding these challenges is the first step toward recognizing why going digital isn't just beneficial—it's imperative.
The Problems with Paper-Based Assembly Instructions
Let's cut to the chase: paper-based work instructions are holding you back. They're time-consuming to create, a resource drain, and they're causing a cascade of overlooked problems you can't afford to tolerate any longer. These issues aren't just annoying; they're damaging your bottom line and your reputation. Let’s walk through how a manual, paper-based approach to work instructions is sabotaging your assembly process:
- Manual, Time-Consuming Creation Process: Manufacturing might be the only industry where people will assemble rockets to shoot into space or high-end electric vehicles while holding pieces of paper giving them instructions on what to do next. To create these work instructions engineers spend countless hours taking screenshots of CAD models, snapping photos on the shop floor and annotating files.
- Lack of Scalability & Version Control Issues: These manual methods are one-offs. Need to update instructions for a product revision? Start from scratch. Launching a new product line? Prepare to invest the same tedious effort all over again. Using the same parts in a new build? Add in the unique assembly notes for each part all over again. This approach isn't efficient and hampers your ability to scale operations efficiently.
- Dependence on Tacit Knowledge: Employee turnover is a reality. When experienced workers leave or retire, they take with them years of hard-earned insights. Imagine a seasoned technician who has been assembling products flawlessly for decades. He "just knows" how everything fits together. But what happens when he retires? His invaluable knowledge walks out the door with him.
- Fragmented Knowledge: Work instructions and tacit knowledge that is successfully documented in a paper-based approach to work instructions ends up fragmented across Microsoft Word, Powerpoint, CAD software and a number of other tools, dispersing critical assembly knowledge and increasing the risk of oversights and missteps in the assembly process.
- Inconsistency and Variance: Without standardized work instructions that capture tacit knowledge on assembly methods, each worker becomes a solo act, interpreting assembly methods in their own way. This lack of uniformity leads to variations in the final product—some units might meet quality standards, while others fall short.
- Increased Assembly Errors and Rework and Reputational Costs: Increased assembly errors from paper-based work instructions lead to expensive rework costs and delays in final delivery of the product. That’s on top of the reputational damage that occurs from delivering an incorrectly assembled or even faulty product to customers.
The Benefits of Digital Assembly Instructions
Embracing digital work instructions isn't just about eliminating paper; it's about transforming your entire assembly process into a more efficient, modular and future-proofed system all while saving time and improving quality control. The benefits of digital work instructions include:
- Capturing Tacit Knowledge: Digital platforms enable you to document the expertise and knowledge of your most seasoned workers. By capturing their insights, notes, and best practices, you create a living repository of knowledge that benefits current and future employees alike.
- Standardization: With digital instructions, every worker follows the same optimized procedures. This uniformity reduces variability, enhances product quality, and ensures compliance with industry standards.
- Modularity and Reusability: Digital instructions are inherently modular. Components and tacit knowledge documented once can be reused across multiple products.
- Real-Time Updates & Version Control: In a digital system, changes are instantaneous and digital platforms maintain a history of revisions, allowing you to track changes over time. This transparency is invaluable for audits, compliance, and continuous improvement efforts.
- Rich Animations: Digitizing work instructions enables you to embed detailed animations and visualizations of your assembly process in action to assist your engineers and technicians throughout complex assembly processes.
- Easy Access: Digital instructions are accessible anytime, anywhere, on any device—be it a tablet on the shop floor or a computer in a remote office.
How Dirac’s BuildOS Can Digitize Your Work Instructions and Supercharge Your Digital Transformation
At Dirac, we understand the challenges of modern manufacturing. That's why we've developed BuildOS, a cutting-edge platform designed to revolutionize your assembly process.
Automated Instruction Creation
From CAD to Work Instructions in Hours, Not Days: BuildOS transforms your CAD files into detailed, step-by-step work instructions with minimal manual intervention. By automating the sequence and animations, we drastically reduce the time engineers spend on creating work instructions.
Applying the 80/20 Rule: We automate 80% of the work instruction creation process. This efficiency allows your team to focus on the critical 20%—infusing the instructions with tacit knowledge and nuanced expertise that only human experience can provide. The beauty of adopting BuildOS is that over time you can eat away at this 20% pool of tacit knowledge by capturing and associating this tacit knowledge directly with specific parts and assembly procedures.
Visualizing the Assembly Process
Dynamic 3D Visualizations: BuildOS doesn't just provide static images; it generates interactive 3D animations that bring the assembly process to life. Workers can visualize each step in motion, enhancing understanding and reducing the risk of errors.
Enhanced Clarity: Complex assemblies become manageable as workers can rotate, zoom, and explore the 3D models, ensuring they grasp every detail before commencing physical assembly.
Capturing Tacit Knowledge
Associations Between Parts and Context: Our platform enables you to link expert notes, tool requirements, and safety precautions directly to specific parts and assembly steps. This feature ensures that critical tacit knowledge is systematically captured and readily accessible.
Knowledge Reusability: Once this information is embedded, BuildOS automatically applies relevant notes and tools when those parts are used in future projects, enhancing efficiency and consistency across the board.
Real-Time Feedback Loops
Interactive Platform: BuildOS facilitates immediate feedback from the assembly team. If a worker encounters an issue or identifies a potential improvement, they can flag it within the system. Engineers and managers receive instant notifications, allowing for swift action.
Continuous Updates: This dynamic communication loop ensures that work instructions evolve in real-time, continuously improving and adapting to on-the-ground realities.
Support and Onboarding
Dedicated Onboarding Team: Transitioning to a new system can be challenging, but with Dirac's team engineers and digital manufacturing experts, you're never alone. We provide hands-on support to ensure your team is confident and proficient with BuildOS.
Customer Success Team: Post-implementation, our dedicated engineers are just an email or call away. Whether you need troubleshooting assistance or advice on best practices, we're here to help your organization thrive.
Step-by-Step Roadmap to Digitize Your Work Instructions and Transform Your Assembly Process
Embarking on this transformation journey to digitize your work instructions is a move that requires careful planning and execution. Fortunately with BuildOS our customers have been able to go from first call to roll-out of buildOS in as little as 6 weeks without the help of any third-parties or systems integrators. When it comes to the world of manufacturing software that is lightning speed!
Here’s our suggested framework for how to navigate the digitization of your work instructions process effectively:
1. Assessment: Evaluate Current Pain Points
Spend 1-3 days speaking with hardware engineers and technicians across your manufacturing organization to get a quick rundown of where paper-based work instructions are causing problems in your assembly process. Look for pain points that can be quantified such as:
- **Errors from Outdated Instructions: **Quantify the impact of mistakes stemming from obsolete documents.
- Time Lost in Creation and Updates: Calculate the hours spent on manually producing and revising instructions.
- Knowledge Loss Due to Turnover: Assess how staff changes have affected productivity and quality over the recent past.
- Identify Stakeholders: Recognize which members of your team are involved with the creation, update and distribution of work instructions.
2. Planning: Set Objectives & Timelines
With any transformation plan that involves adopting new tools or changing workflows, setting clear targets and defining the destination are critical for aligning the whole organization. Some typical objectives and KPIs our clients have tracked in the past include:
- Reduce Errors by X%: Set a target for how much you hope to reduce the error rate during your assembly process.
- Reduce Time to Create Work Instructions Y%: Digitizing the creation of work instructions significantly reduces the time it takes to create new work instructions.
- Decrease Assembly Time by Z%: Streamlined work instructions can lead to efficiency gains throughout your assembly process.
- Improve Quality Control by XY%: Quality control issues should reduce with digital work instructions enabling more accurate assembly workflows
- Institutionalize All Assembly Knowledge by [Specific Date]: Establish a timeline for capturing and documenting all the tacit knowledge and expertise in your organization
3. Preparation: Embedding Your Knowledge into BuildOS
Dirac’s BuildOS was designed and built by former hardware engineers and is purpose-built for digitizing work instructions. Drop in a CAD file and let the product do the rest. BuildOS generates path plans, sequences assembly steps, produces 3d renderings and animations, and generates text for each instruction—all automatically.
With BuildOS the end-to-end process for creating digital work instructions is 80% automated on day one. The remaining 20% involves documenting your team’s tacit knowledge and uploading it into BuildOS.
Upload Your CAD Files:
- Leverage User-Friendly CAD Tools to Define Clusters and Assembly Constraints: BuildOS provides access to a set of inbuilt basic CAD tools tailored for work instruction creation, eliminating the need for specialized CAD software and advanced CAD expertise. Define groups of identical parts that are installed together as clusters which will inform BuildOS of your assembly constraints.
- Automatic Animation Generation: BuildOS creates detailed animations for each assembly step automatically.
- Simulation Runs: The platform conducts multiple simulations based on the CAD files and your assembly constraints to recommend the most efficient assembly sequence.
Add Contextual Knowledge and Adjust for Mechanical Assembly:
- Edit Part Trees and Hierarchies: Customize the assembly structure to align with practical considerations on the shop floor and your actual assembly workflow.
- Create and Modify Sub-Assemblies: Break down complex assemblies into manageable steps for clarity.
- Attach Notes and Tools: Embed critical information directly into the relevant parts and steps, ensuring technicians and engineers have all the necessary details at their fingertips.
4. Training: Equip Your Team
Onboarding Sessions and Phased Deployment:
- Hands-On Training: Schedule interactive sessions with Dirac's experts to familiarize your team with BuildOS features and functionalities.
- Pilot Project: Select a specific product line or assembly to implement first, allowing for adjustments and learning before a full-scale rollout.
- Company-wide Rollout: After adequate training and the success of your pilot project, rollout BuildOS across your organization and assembly lines.
5. Evaluation: Monitor and Refine
Continuous Support:
- Ongoing Assistance: Take advantage of our customer success team for troubleshooting and optimization advice.
- Resource Materials: Utilize our library of tutorials, guides, and webinars to institute company-wide best practices and reinforce learning.
Gather Feedback and Measure Performance:
- Collect Input from All Stakeholders: Encourage engineers, technicians, and assembly workers to share their experiences and suggestions on the early performance of digital work instructions and any snags in adoption.
- Track Key Metrics: Monitor error rates, assembly times, and quality control indicators to gauge the impact of digital work instructions.
Real-Life Success Story: Ancra Aircraft's Transformation
Ancra Aircraft, a leading aerospace OEM, equips over 60% of the world's aircraft freighter fleet with main deck cargo loading systems. Faced with the challenges of paper-based work instructions, Ancra sought a solution to streamline their assembly process and maintain their competitive edge.
By implementing BuildOS, Ancra transitioned seamlessly from paper to digital work instructions. The results were remarkable:
- Time Savings: Reduced the time spent on creating and updating work instructions from 4 days to just 1 hour.
- Knowledge Retention: Ancra has captured and documented tacit knowledge on its assembly process and preempted the risk of knowledge loss due to retirement or turnover.
- Enhanced Quality: Standardized procedures improved product consistency and customer satisfaction and reduced costs due to rework and waste.
Ancra's success showcases the transformative power of digital work instructions and serves as a blueprint for other organizations aiming to modernize their operations. Read more about how Ancra uses BuildOS here!
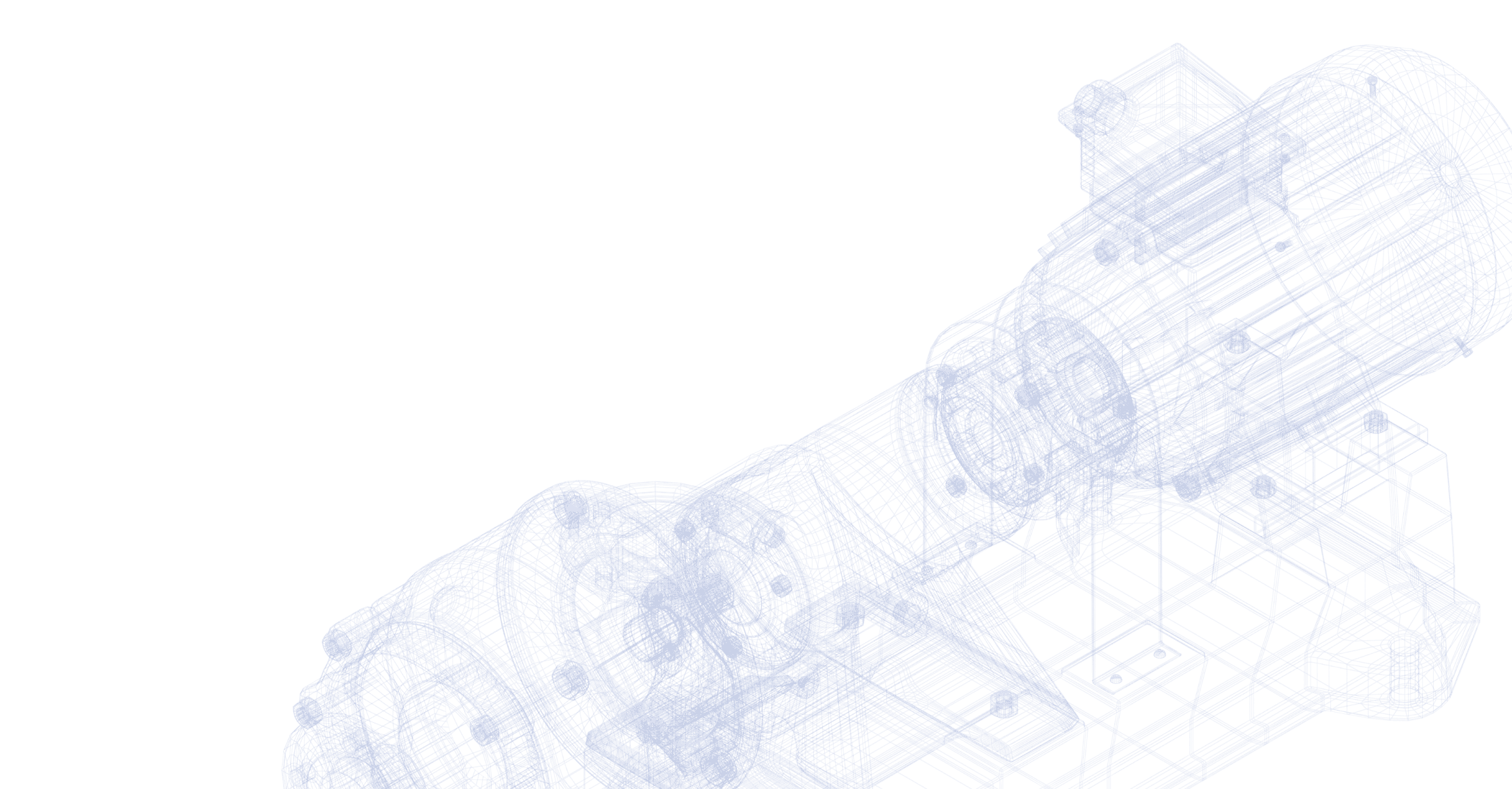
Dirac is the Assembly Company of the future.
350 5th Ave Ste 4720, New York, New York