Future-Proofing Agricultural Machinery Manufacturing: The Power of Automated Work Instructions
Transform Your Shop Floor: Streamline Production, Cut Errors, and Boost Efficiency with Digital Work Instructions
January 20, 2025
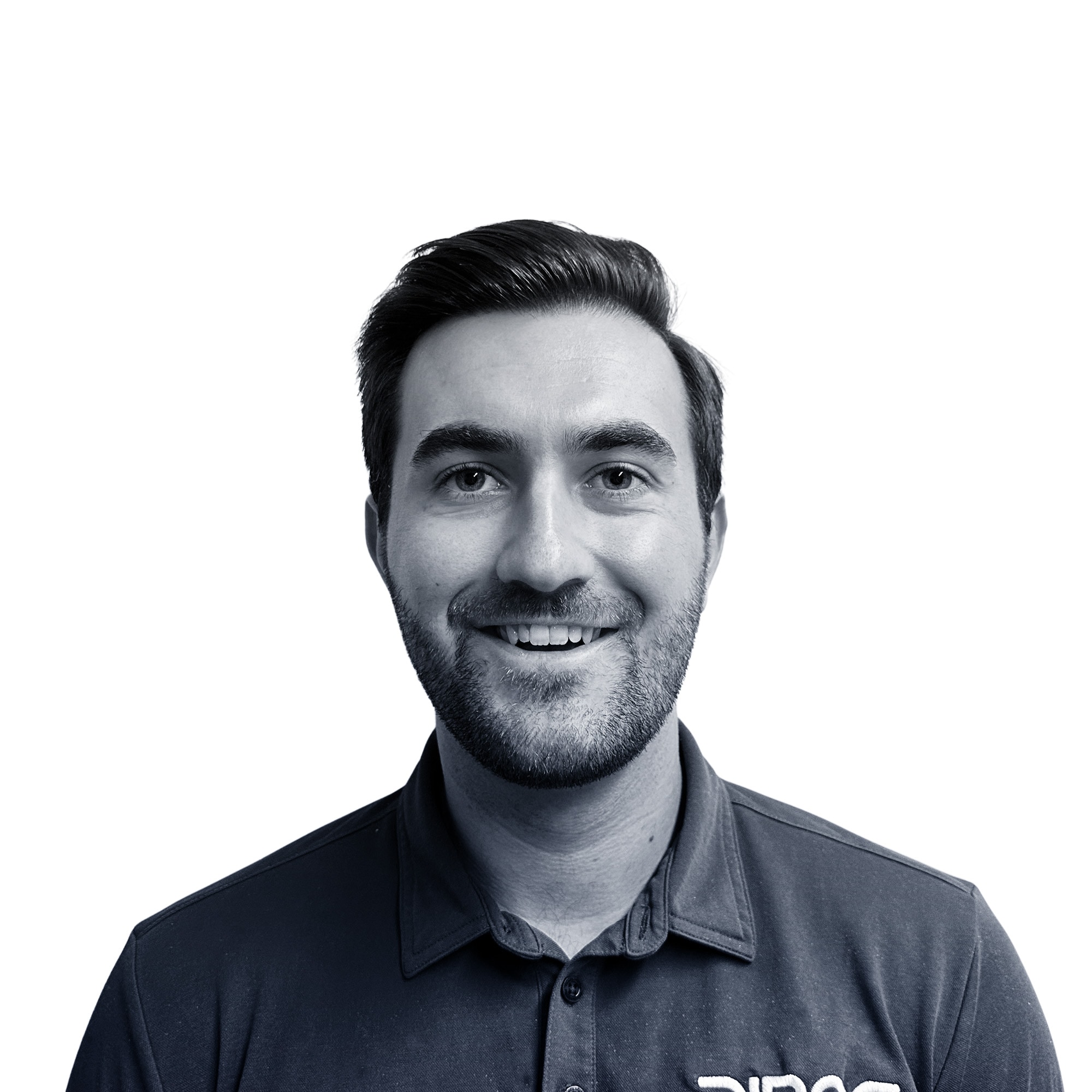
Introduction
Let's face it: in the high-stakes world of agricultural machinery manufacturing, the assembly process is where the rubber meets the road, literally. You’re building complex machines designed to perform under extreme pressure, and the accuracy of your assembly directly impacts your bottom line. But if your team is still relying on outdated paper-based work instructions to assemble your cutting-edge equipment, you’re not just working with one hand tied behind your back—you’re practically sabotaging your own success.
These archaic paper-based processes are a massive roadblock, creating bottlenecks, increasing errors, and racking up unnecessary costs. It’s time to recognize that clinging to the past is preventing your company from reaching its full potential. But there is an answer: Automated work instructions. This blog post is your wake-up call, revealing why digital, automated work instructions are not just a “nice-to-have,” they are the key to future-proofing your entire manufacturing operation.
The Challenge: Paper-Based Instructions are Holding Back Agricultural Machinery Manufacturers
The agricultural machinery sector is known for its rugged innovation, but when it comes to assembly, many companies are still stuck with archaic manufacturing paradigms. One of the best examples of that are paper-based work instructions; a system that is not only antiquated but fundamentally broken. Let’s break down exactly how this manual approach is actively undermining your success.
- The Inefficiency of Manual Creation: Your engineers are spending countless hours manually creating work instructions. They are taking screenshots from CAD models, annotating them, snapping photos on the shop floor and then manually compiling all of this into a document. This is not just a waste of time; it’s a misallocation of your most valuable resources. And, to add insult to injury, with every new product or revision of an existing product, they have to start this tedious process all over again. This manual process is time-consuming, resource intensive and very inefficient.
- Scalability and Version Control Nightmares: In a modern manufacturing environment, flexibility is key. But with paper-based instructions, even small changes are a monumental pain. Need to update instructions for a product revision? Prepare to start from scratch. Launching a new product line? Prepare for another marathon of manual creation. Using the same parts in a new build? Be prepared to manually enter the same notes for each individual part. This approach isn't scalable and makes it nearly impossible to adapt to changes quickly and efficiently. And let’s not even talk about version control. With paper, how can you be sure that every single employee is using the latest version of the instructions? The answer: you can’t, which inevitably leads to costly errors.
- The Reliance on Tacit Knowledge: Paper-based work instructions fail miserably at capturing the undocumented knowledge of your seasoned employees. We're talking about the “tribal knowledge,” the countless little tips and tricks that veteran technicians have learned over the years. Imagine a technician who can assemble a complex component blindfolded. He just knows how everything fits together based on years of experience. But how is that knowledge captured in a paper-based work instruction? The answer: it’s not. And what happens when that seasoned employee retires or leaves the company? That invaluable knowledge simply walks out the door. It’s a recipe for disaster.
- Fragmentation and Inconsistency: When paper-based instructions are the norm, critical assembly knowledge often ends up fragmented across different tools like Word, Powerpoint and CAD software, making critical assembly knowledge difficult to access. And without standardized work instructions that capture the tacit knowledge, each worker ends up interpreting assembly methods in their own way, leading to inconsistencies and variations in the final product. Some units might meet the required quality standards, while others fall short of the mark. This lack of uniformity creates additional problems in manufacturing, leading to quality control issues that can be costly and damaging to your reputation.
The Cost of Sticking with Paper: Errors, Rework, and Reputational Damage
The problems with paper-based instructions aren’t just theoretical—they have a direct and meaningful impact on your manufacturing operations.
- Increased Assembly Errors: Let’s be clear: outdated or ambiguous instructions lead directly to assembly errors. If your team doesn’t have clear, up-to-date instructions, mistakes are inevitable. And when you’re dealing with complex machinery like agricultural equipment, even small errors can have catastrophic consequences in the final product, and can create costly and unnecessary delays in your production timeline. The bottom line: paper-based instructions create an environment that is ripe for mistakes.
- Expensive Rework and Delays: Assembly errors are not cheap, because they lead to time-consuming and costly rework. If you’re spending time and money fixing problems caused by errors, you’re wasting valuable resources that could be used elsewhere in your business. And that’s not even mentioning the delays that stem from this process of rework, which can ultimately throw off the production timeline entirely.
- Reputational Damage: Delivering a faulty product is not just a financial hit; it's a hit to your reputation. In today’s market, customers expect high-quality, reliable products. And if you can't deliver, they’ll go to your competitors. The reality is that poor assembly quality can damage long-term relationships with your clients, and can erode trust in your brand.
The Solution: The Benefits of Digital Assembly Instructions
The good news is that there's a better way. Ditching paper-based instructions is not just about eliminating an outdated process; it’s about transforming your entire assembly process into an efficient, modular and future-proofed system that saves you time and improves the quality of your products.
- Capturing and Standardizing Tacit Knowledge: Digital platforms allow you to finally capture the expertise and undocumented knowledge of your most seasoned employees. By documenting their insights, their tips and tricks, and their best practices, you’re creating a dynamic knowledge base that can benefit every single worker in your organization. You’re no longer reliant on tribal knowledge alone, and you’re actively building a living repository of assembly knowledge that will serve your organization for years to come.
- Standardization and Consistency: With digital work instructions, every worker follows the exact same, optimized procedures. This uniformity drastically reduces variability, enhances product quality, and ensures compliance with industry standards. Standardized work instructions are not only more efficient, they also guarantee consistent, repeatable results.
- Modularity and Reusability: Digital instructions are modular by nature. Components and tacit knowledge documented once can be easily reused across multiple products. This saves time, minimizes rework, and ensures that your processes are constantly evolving for optimal performance. Knowledge once documented becomes a reusable resource in all of your manufacturing processes, boosting efficiency across the board.
- Real-Time Updates and Version Control: With a digital system, any changes can be made instantaneously, and all employees will have access to the latest version of the instructions. Digital platforms also maintain a complete history of revisions, which allows you to track changes over time. This transparency is critical for audits, compliance, and continuous improvement efforts.
- Rich Animations and Visualizations: Digitizing work instructions enables you to embed detailed animations and 3D models of your assembly process. These visual aids are essential for understanding complex procedures and reduce ambiguity, while also helping workers to visualize each step, improving their comprehension and reducing the likelihood of error.
- Accessibility and Flexibility: Digital instructions are accessible at any time, on any device, and from any location. Whether it's a tablet on the shop floor or a computer in a remote office, your team can access the information they need. This means that you’re no longer tied to physical documents, and all the relevant information is available to all of your employees wherever they may be.
How Dirac’s BuildOS Can Digitize Your Work Instructions
Now, let's get down to business: How can you actually implement these changes? Dirac’s BuildOS is the answer. It's a cutting-edge platform specifically designed to revolutionize your assembly process.
- Automated Instruction Creation: BuildOS can transform your CAD files into detailed, step-by-step work instructions in hours, not days. By automating the creation of work instructions you drastically reduce the time your engineers spend on manually creating and updating instructions. This allows them to focus on higher-value work.
- Visualizing the Assembly Process: BuildOS isn’t just about static images; it generates interactive 3D animations that bring the assembly process to life. Workers can rotate, zoom, and explore the 3D models, ensuring they fully grasp every detail before they even begin the physical assembly. This greatly enhances clarity, particularly for complex assemblies.
- Capturing Tacit Knowledge: Our platform allows you to link expert notes, tool requirements, and safety precautions directly to specific parts and steps in the assembly process. Once this information is embedded, BuildOS automatically applies it whenever those parts are used in future projects. This feature ensures that the critical knowledge of your experienced workers is systematically captured, easily accessible, and reusable across the organization.
- Real-Time Feedback Loops: BuildOS is designed to encourage immediate feedback from your assembly team. If a worker encounters a problem or has suggestions for improvement, they can flag it directly within the system. Engineers and managers will receive instant notifications, allowing for quick action and continuous improvement of your instructions. This ensures that your instructions are always evolving to reflect the most up-to-date and efficient practices on the shop floor.
Conclusion
The agricultural machinery manufacturing industry is under constant pressure to improve efficiency, reduce costs, and maintain the highest standards of quality. To address these challenges and future-proof your operations, adopting automated work instructions isn't just an option, it's a necessity. Stop relying on outdated paper-based instructions. It’s time to embrace the future. Dirac’s BuildOS isn’t just a tool; it’s a comprehensive solution that allows you to reduce errors, streamline your assembly processes, and capture the critical knowledge that lives within your organization.
Take the First Step Today
Schedule a free consultation and discover how BuildOS can digitize your approach to creating work instructions and transform your assembly operations to help your agricultural machinery business thrive into 2025 and beyond.
The future of agricultural machinery manufacturing is digital—don't get left behind.
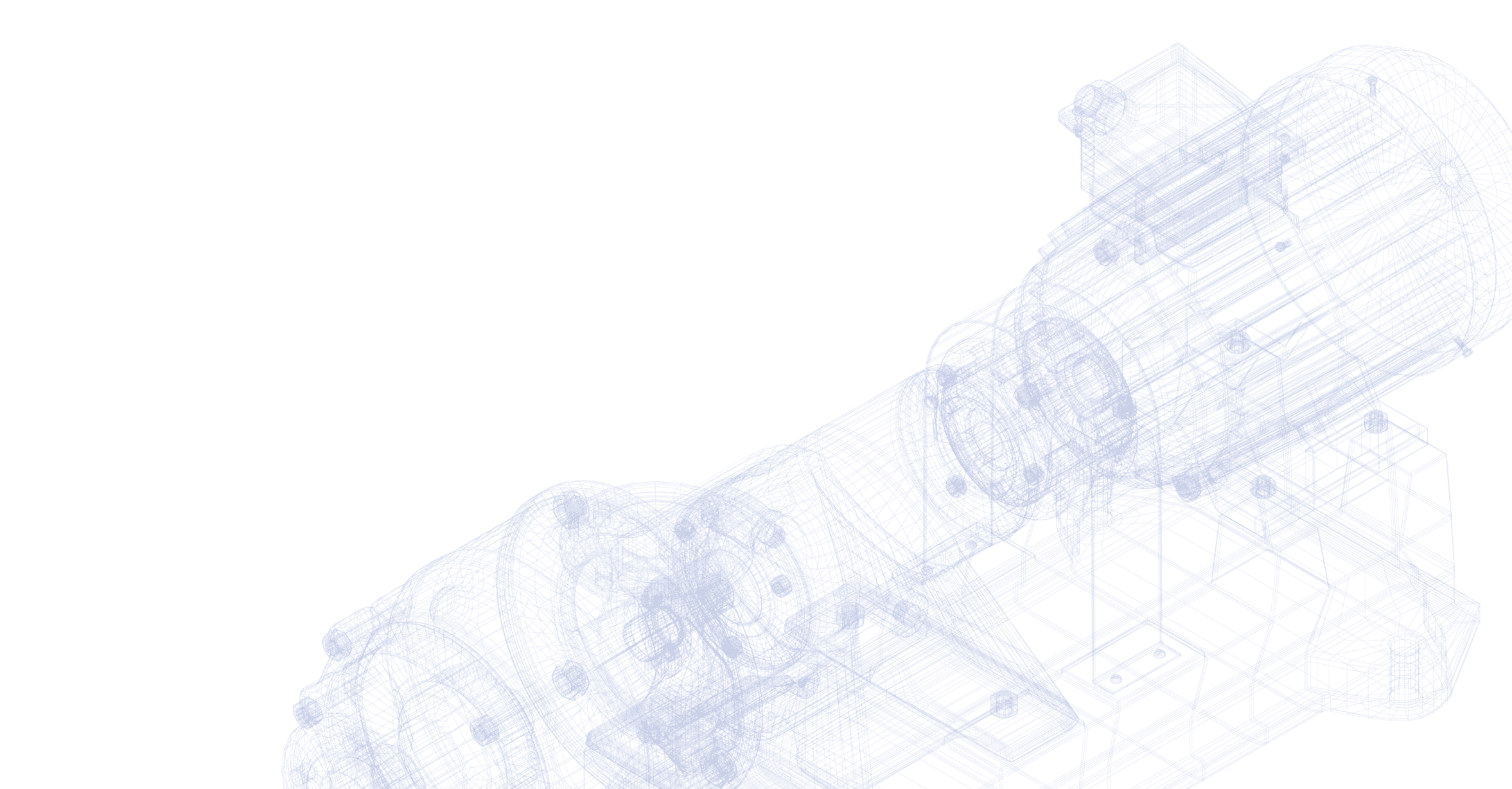
Dirac is the Assembly Company of the future.
350 5th Ave Ste 4720, New York, New York